"Integrated Design of the Central Beam Pipe and Support of Vertex Detector Elements"
The beam pipe for SiD is expected to consist of a short, central portion of radius approximately 12 mm, conical portions which grow in radius and extend symmetrically in each direction from the central portion, and guided bellows which accommodate thermal contraction and misalignment of the detector with respect to accelerator beam line elements. The central portion is expected to be thin-walled (0.4 mm or less) beryllium. Regions of the conical portions are also expected to be beryllium, but to have a greater wall thickness (approximately 1 mm). Liners (presently suggested to be titanium 0.025 to 0.075 mm thick) are required. Shield masks made of tungsten or similar material are expected near the outer ends of the conical portions. The specifications for shielding materials will be developed under a separate R&D proposal submitted by T. Markiewicz. Participants in the two proposals will interact closely to ensure an integrated beam pipe design.
One model for servicing of the vertex detector assumes that the vertex detector is fully supported from the beam pipe. Providing such support places constraints on the beam pipe wall profile and thickness. Minimizing the consequences of beam pipe material on physics capabilities of the detector requires careful selection of beam pipe materials and thicknesses.
During the first year of R&D, analytic and finite element calculations of beam pipe deflections and stresses will be made as an aid in specifying the desired beam pipe radial profile, wall thickness, and materials. Initial estimates of required shielding materials will be taken into account. A proposal will be developed which specifies the profile, wall thickness, and materials of the beam pipe taking into account shielding requirements. That proposal will be discussed with industry to aid in understanding its feasibility and the extent to which specialized fabrication procedures would need to be developed. Contracts will be issued to begin fabrication of representative portions of the beam pipe to develop those fabrication procedures. Deliverables at the end of the first year will consist of the following:
1. beam pipe deflections and stresses as a function of longitudinal position
2. a proposal for beam pipe radial profile, wall thickness, and materials which takes into account initial estimates of shielding requirements
3. an iteration of beam pipe deflections and stresses as a function of longitudinal position for that proposal
4. an evaluation, based upon contacts with industry, on the feasibility of the proposed design
5. initiation of fabrication of prototypes of critical regions of the beam pipe.
During the second year of R&D, prototypes representing each portion of the beam pipe will be completed and tested, designs will be iterated, and a prototype beam pipe made of stainless steel will be obtained and tested. Designs for tungsten masks (or equivalent) and guided bellows will be developed. Deliverables at the end of the second year will consist of the following:
6. prototypes representing each critical region of the beam pipe
7. test results of those prototypes
8. an evaluation of fabrication techniques and procedures for each region of the beam pipe
9. iteration of the design to take into account a more complete knowledge of required shielding materials
10. a mechanical prototype of the beam pipe based upon stainless steel
11. measurements of deflections and stresses of the stainless steel beam pipe
12. designs for guided bellows.
During the third year of R&D, guided bellows will be obtained and tested, then added to the stainless steel beam pipe. Deflections of the full assembly of stainless steel beam pipe, bellows, and simulated masks will be measured. Designs and fabrication drawings for the final beam pipe will be completed. Procedures will be developed for acceptance testing, including a bake-out and leak check. Budgetary quotes will be obtained based upon those drawings and associated specifications. Deliverables at the end of the third year consist of:
13. a full stainless steel beam pipe, including guided bellows and simulated tungsten masks
14. measurements of deflections under load of that beam pipe
15. full fabrication drawings of a final beryllium beam pipe
16. procedures for beam pipe acceptance testing, including a bake-out and leak check
17. a budgetary cost estimate for that beam pipe.
Please address the following questions in your statement.
- What are the goals of this R&D project. How does this R&D project address the needs of one or more of the detector concepts?
- If there are multiple institutions participating in this project, please describe the distribution of responsibilities.
- Are there significant recent results?
- What are the plans for the near future(about 1 year)? What are the plans on a time scale of 2 to 3 years?
- Are there critical items that must be addressed before significant results can be obtained from this project?
- Is the support for this project sufficient? Are there significant improvements that could be made with additional support?
This topic: ILC/WWS
> WebHome >
Instructions >
CreateProjectPage >
MdiFnalIntBeamPipe > MdiFnalIntBeamPipeStatement
Topic revision:
21 Dec 2005, DanPeterson
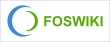
Copyright © by the contributing authors. All material on this collaboration platform is the property of the contributing authors.
Ideas, requests, problems regarding CLASSE Wiki?
Send feedback