"R&D Towards a Long Shaping-Time Silicon Strip Central Tracker"
The goal of the long shaping-time silicon sensor
readout project is to develop readout and data-handling
architecture optimized for an ILC detector. Although
motivated by an interest in reading out long silicon
sensor ladders (to minimize the complexity and material
burden of the readout electronics), this R&D is also
applicable to the readout of short modules. All
current detector concepts include a substantial area
of silicon strip detectors; thus, this R&D is globally
applicable to Linear Collider detector R&D. Although
our group's nominal affiliation is with the SiD concept
study, we also consider ourselves contributors to the
GLD and LDC efforts, and are lead participants in the
SiLC group.
The Santa Cruz Institute for Particle Physics
(SCIPP) hardware effort on silicon microstrip readout
began with the creation of a detailed simulation
of the development, amplification, and digitization
of signal pulses induced by incident charged particles.
This simulation guided the choice of several aspects
of the readout chip design. In particular, the
simulation indicated that efficient readout with
low occupancy for a 167 cm ladder (one-half the length
of the outermost layer of the baseline SiD tracker)
could be achieved with a 3 microsecond shaping time.
Chosen for the prototype ASIC, this shaping time would
also permit timing to within a few crossings of the LC
beams, more than adequate for the expected occupancy
levels.
The simulation also suggests that, given the extent
of fluctuations in the deposited energy, no information
would be lost by using the essentially logarithmic
time-over-comparator-threshold response to estimate
analog pulse heights. However, in order to avoid
losing neighboring channel information, a second,
lower-threshold comparator needs to be applied to
channels neighboring a channel whose pulse-height
excites the nominal comparator, whose higher threshold
it set to limit noise occupancy. This dual-comparator
strategy allows
for better than 7 micron resolution for 167 cm ladders
(see Figure). It is important to note that, should
the SiD design incorporate short, tile-like ladders,
this resolution would improve substantially.
The dual-comparator "LSTFE2" front-end ASIC is currently
undergoing testing at SCIPP.
The amplifier output in mV in response
to a calibration step in shown in a second
figure (1 MIP is
corresponds to about a 3.5 mV step). As designed,
the response
quickly saturates into its time-over-threshold
response; such a high gain is chosen to avoid
the effect of process variations on the
application of the threshold to sub-MIP signals,
which can degrade the effective noise performance
of the chip for a multi-channel system.
The SCIPP group has also developed a back-end
strategy for buffering and reading out the comparator
output. Leading and trailing edges
are stored for all high-comparator transitions,
as well as low-comparator transitions that are
sufficiently close in time and space to high-comparator
transitions. The simulation has suggested that a
400 nsec readout clock (roughly 10% of the shaping
time) is adequate to preserve time-over threshold
information. We have tested this strategy in a
simulation of the innermost layer, for a conservative
(high) rate of noise and background-hit occupancy,
as a function of the low-comparator threshold.
The result of this study is shown in the third figure.
The predicted data rate of less than 10 kbit per
LC machine spill per 128 channel chip scales up
to an overall data rate of less than 0.5 GHz to
be transmitted off the detector through optical
fiber (this would increase by roughly a factor
of 10 for short strips), which is a very modest
data rate.
SCIPP continues to test the prototype LSTFE2
chip, and is working towards a additional
submissions of refined
LSTFE designs that will further
optimize noise performance as well as expand
the channel multiplicity from eight to 128 channels.
Within the next year, we hope to have this refined
and expanded ASIC under testing at SCIPP, to have
verified our digital architecture scheme, and to
have explored the properties of the existing LSTFE2
chip on a 1-2 meter long silicon sensor assembly,
confirming signal-to-noise projections and
timing resolution.
We hope to use the LSTFE chip in a testbeam run
in late 2007 or early 2008. In this testbeam
run, we will need to demonstrate the power-cycling
capabilities of the ASIC, measure efficiency and
space-point resolution as a function of incidence
angle, and verify the back-end architecture in
a realistic environment. While we plan at this
point to still have the back-end architecture
implemented on an FPGA, incorporation of this
digital logic onto the amplifier/comparator
ASIC should be relatively straightforward.
Although supported with approximately $50,000
per year of DOE LCRD funding, and some
support from the SCIPP base DOE grant, we believe
that we will need an augmentation of funds to
carry this work out. Design and fabrication of
one or two additional prototype ASIC's, and
the preparation for and execution of a testbeam
run, is only partially covered by existing funding
levels. We will need some additional staff,
student, equipment, and travel support to be
assured of success.
Please address the following questions in your statement.
- What are the goals of this R&D project. How does this R&D project address the needs of one or more of the detector concepts?
- If there are multiple institutions participating in this project, please describe the distribution of responsibilities.
- Are there significant recent results?
- What are the plans for the near future(about 1 year)? What are the plans on a time scale of 2 to 3 years?
- Are there critical items that must be addressed before significant results can be obtained from this project?
- Is the support for this project sufficient? Are there significant improvements that could be made with additional support?
This topic: ILC/WWS
> WebHome >
Instructions >
CreateProjectPage >
TrackUCSCLong > TrackUCSCLongStatement
Topic revision:
06 Nov 2005, BruceSchumm
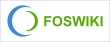
Copyright © by the contributing authors. All material on this collaboration platform is the property of the contributing authors.
Ideas, requests, problems regarding CLASSE Wiki?
Send feedback